- Huyett Marketing Department
- 04/21/2022
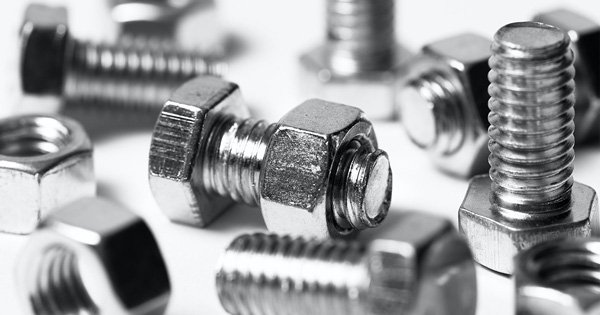
Joints created by nuts and bolts are all around us. They are in our cars, houses, furniture, and appliances. They are a vital component of most structures, vehicles, and industrial machines. Although we tend to take nuts and bolts for granted, a bolted joint is a complex mechanism. When buying nuts and bolts, it is important to understand how they work and how to choose the right combination of parts for your application.
How Do Nuts and Bolts Work?
A typical bolt has two main components: a shaft and a head shaped to fit a tool like a wrench. Bolts have an externally threaded shaft. The shaft may be entirely threaded, or it may be divided into threaded and unthreaded portions. The unthreaded portion is often called the shank or the grip length. The most common bolt heads are hex-shaped. However, other variations exist for specialty applications.
A nut is a fastener with an internal thread and an external surface shaped to fit a tool. Like bolt heads, modern nuts are usually hex-shaped. Nuts are screwed onto bolts to form a bolted joint.
The purpose of a bolted joint is to prevent parts from moving relative to each other. Each bolt and nut component plays a role.
- The bolt's shaft prevents the parts from moving laterally (sideways) relative to each other.
- The bolt's head and the nut prevent parts from moving away from each other.
- The clamping force generated by a correctly torqued nut and bolt joint prevents parts from moving radially (rotating relative to each other).
When installing a bolt with a nut, there are two main stages. In the first stage, the nut screws easily onto the bolt until the bolt head and the nut are in contact with the surface of the joined parts.
In the second stage, it becomes much harder to tighten the nut. That's because further tightening—or torquing—elongates the bolt. Like an elastic band, this elongation generates tension in the bolt called the preload force. The preload force creates a clamping force that acts on the joined parts, holding them together.
When installing a nut and bolt, it's essential to achieve the correct preload force. Or, to put it another way, you need to apply the proper amount of torque. Inadequate preload can cause parts to move relative to each other or the nut to unscrew from the bolt. Excessive preload can strip the bolt's threads, causing the joint to fail.
A Brief Introduction to Nut and Bolt Thread Standards
Nuts and bolts are threaded fasteners, where a thread—more properly known as a screw thread—is a helical ridge on one component designed to mesh with a similar thread on another component. The thread determines how the joint performs, its strength, and which nut or bolt is suitable for a particular job.
Before we explore the specific features of nuts and bolts, let's look at the basic vocabulary used to describe threads.
- Thread crest: the top of the helical ridge, the helix-shaped raised structure formed by the thread as it winds along the bolt's shaft.
- Thread root: the low point between two crests.
- Thread flank: the side of the thread's ridge between the root and the crest.
- Thread angle: the angle of the V-shaped groove between two crests.
- Helix angle: the angle of the thread relative to the axis of the shaft.
- Thread pitch: the distance between corresponding points on adjacent thread surfaces measured in-line with the shaft of a bolt or the hole in a nut. You can also think of pitch as the distance between thread crests measured in a straight line along the bolt or nut.
- Major diameter: the distance between crests on opposing sides of an externally threaded bolt's shaft or between roots on an internally threaded nut.
- Minor diameter: the distance between roots on opposing sides of an externally threaded shaft or crests on an internal thread.

The definition of major diameter and minor diameter differ for external and internal threads. The important point to remember is that the major diameter is always the largest, whether that's root-to-root (internal threads) or crest-to-crest (external threads).
These concepts may look complicated, but many thread features are standardized. For example, the thread angle is 60° in standard nuts and bolts sold worldwide, so it's not a feature buyers typically need to consider.
Thread Standards: UTS vs. ISO
In the U.S., the dominant thread standard is the Unified Thread Standard (UTS), which is overseen by ASME/ANSI and defined in
ASME B1.1 - 2019 Unified Inch Screw Threads. The UTS specifies thread sizes, profiles, and tolerances. They also mandate the 60° thread angle, as well as other features like the profile of crests and roots.
The UTS uses inch-based measurements to describe threads. In contrast, you may encounter the ISO standard, which uses metric measurements. A metric standard thread has the same thread profile and thread angle as a UTS thread but is measured in millimeters.
Thread Standards: UTS vs. ISO
The UTS determines how to describe nut and bolt thread measurements. For example, you can find hex bolts on huyett.com with the product name "
Hex Bolt 5/16-18 x 1 CS ZN". The thread designation is the cluster of numbers immediately following "Hex Bolt." In this case: 5/16-18.
The first two numbers—5/16—are an inch measurement of the thread's major diameter, the distance between thread crests measured across the bolt. This bolt has a thread that is 5/16 of an inch across its widest points.
Threads with a major diameter of 1/4 inch or larger use the inch measurement in their designation, as in the example bolt. If the major diameter is smaller than 1/4 inch, the designation uses an integer between 0 and 12 specified in the UTS. For example, a #5 thread has a major diameter of 0.1250 inches.
The second number—18—is the number of threads per inch (TPI). This indicates the number of complete thread revolutions that fit into an inch along the shaft. Our thread vocabulary guide mentioned thread pitch—the distance between threads. Pitch and TPI are related; pitch is the reciprocal of TPI. The example bolt has 18 threads per inch, which means the pitch is 1/18 or approximately 0.055 inches.

TPI and thread pitch are technically different, but the terms are often used interchangeably. Neverless, if you are buying nuts and bolts with inch sizes, you can be confident that the number described as the pitch indicates the TPI.
Metric thread designations are different in two main ways. First, the major diameter is measured in millimeters. Second, metric thread designations indicate the thread pitch in millimeters instead of the TPI. For example, a metric nut with the thread designation M8x1.25 has a major diameter of 8 mm and a thread pitch of 1.25 mm.
Threaded Bolts: An Overview
Bolts are one of the most versatile and widely used threaded fasteners. Because bolts are inexpensive, straightforward to manufacture in large numbers, and easy to install with hand tools, they are the number one choice for creating robust joints in industrial applications.
What Are Bolts Made Of?
Most bolts are made of low or medium carbon steel.
Carbon steel bolts are tough enough to accommodate the stress and strain of most applications while remaining straightforward to machine and resistant to breaking under squeezing forces (compression), pulling forces (tension), and forces acting perpendicular to the bolt's axis (shear).
However, carbon steel bolts are not suitable for every application, which is why bolts are manufactured in other materials, including:
- Stainless steel bolts for improved resistance to corrosion.
- Nylon bolts for use with plastic and other softer materials.
What are the Two Types of Threads on Bolts?
When buying threaded bolts, you may find threads described as coarse or fine or with the designation UNC (coarse) or UNF (fine). These refer to the standard threads per inch on a particular thread size. Fine threads have a higher TPI and, consequently, a smaller pitch.
As with other thread properties, the TPI of fine and coarse threads is defined in the Unified Thread Standard. For example, a standard coarse 1/4 inch thread has a TPI of 20, whereas a fine 1/4 inch thread has a TPI of 28. There is also a less common extra fine (UNEF) thread, which would give the 1/4 inch bolt a TPI of 32.
The coarseness of the thread has nothing to do with its quality. Instead, it's a trade-off between different properties provided by higher or lower thread pitches. Coarse threads are harder to strip or cross-thread and faster to install. Finer threads are stronger and less likely to vibrate loose.
Fully Threaded Bolts vs. Partially Threaded Bolts
Bolts are available in both fully threaded and partially threaded variants. Fully threaded bolts require more force to pull out of a joint (pull-out force) because they engage with internal threads along their entire length.
In contrast, partially threaded bolts offer greater shear strength along the non-threaded portion. Shear forces act perpendicular to the axis of the shaft; they often occur when the two parts fastened by a bolt joint try to slide across each other. Threads create weak points which reduce shear strength.
The right bolt for your application depends on the required pull-out strength, shear strength, and the arrangement of threads within the joined parts.
The Principal Types of Threaded Bolt
Hex Bolts
Hex bolts are bolts with a six-sided head. They are by far the most widely used types of bolt. At Huyett, we stock
carbon steel hex bolts and
nylon hex bolts.
U-Bolts
U-bolts are u-shaped bolts with threads on both ends. They are often used with nuts to suspend pipe and conduit or to anchor cylindrical components.
Step Bolts
Step bolts feature a round, low-profile head which provides an increased bearing surface compared to standard hex bolts. Below the head is a square neck which stops the bolt from turning when the nut is tightened. Step nuts are often used to bolt down wood and other softer materials because the larger head spreads the load and decreases the likelihood of the bolt pulling through the material and damaging joint parts.
Step bolts are also used to form steps on communication and electrical towers, where they are secured to a metal streucture with a pair of nuts.
J-Bolts
J-bolts have a threaded shaft and a hooked head. J-bolts are often partially submerged in concrete, where the hook prevents the bolt from pulling out. In reinforced concrete, the hook fits around and grips reinforcing bars (rebar). The threaded shaft protrudes from the concrete, providing a secure fixing point.
L-Bolts
L-bolts are bolts with a shaft bent to a 90° angle, which is why they are often called 90° anchor bolts. L-bolts are used primarily to attach posts, plates, and other fixtures to concrete or masonry foundations.
Eye Bolts
Eye bolts have a threaded shank and a round donut-shaped head. They are often used to attach
lifting and rigging hardware. The threaded shaft is secured in a tapped hole on the load, and a
lifting hook is attached to the eye via a
shackle. Eye bolts are also used to create attachment and suspension points for cables or chains.
Learn more about eye bolts in
How to Install Eye Bolts and Eye Bolt Safety Best Practices.
Threaded Bolts: An Overview
Nuts are internally threaded fasteners used with bolts to form joints between wood, metal, and plastic components. Nuts are also used with other threaded parts, including to secure the pins of
anchor shackles.
What Are Nuts Made Of?
As with bolts, nuts are generally made of carbon steel. Carbon steel nuts work well with carbon steel bolts, but we also stock nuts made of other materials, including:
The Principal Types of Nuts
Hex Nuts
Hex nuts are the most widely used nut. They feature a six-sided external surface and an internally threaded hole for use with matching bolts and other threaded hardware.
Huyett stocks a wide variety of hex nuts, including both standard
inch hex nuts and
metric hex nuts.
Coupling Nuts
Coupling nuts are extra-long nuts used to join externally threaded components. Two threaded parts such as threaded rods or hanger bolts are screwed into the opposing sides of the coupling nut, providing a strong and easily installed joint between parts.
Jam Nuts
Jam nuts are low-profile, half-height nuts used to prevent the loosening of bolted joints. Jam nuts are installed on a bolt or threaded rod before a full-size nut. They are usually tightened to between 25% and 50% of the joint's desired torque. Then, the full-size nut is installed to the joint's final torque. For many modern applications, lock nuts are preferred to jam nuts.
Lock Nuts
Lock nuts, also known as self-locking nuts, prevailing torque nuts, or nyloc nuts, are similar to standard hex nuts with the addition of a nylon or metal insert. The insert deforms when the nut is installed, increasing the prevailing force required to install the nut and its ability to resist loosening. Self-locking nuts with nylon inserts can be reused many times, although standards in some industries mandate minimum prevailing torque requirements for re-used self-locking nuts, including the Federal Aviation Authority's
Acceptable Methods, Techniques, and Practices (AC 43.13-1B).
Learn more about lock nuts in
How to Use Lock Nuts and Lock Washers.
For more information, visit our
Nuts, Bolts, and Screws FAQ or view our full range of industrial fasteners on
huyett.com.