- Huyett Marketing Department
- 03/10/2022
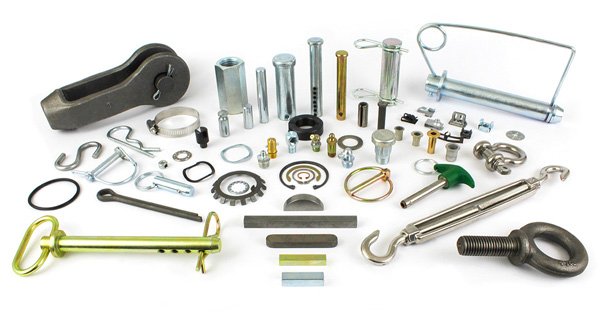
Fasteners are among the most widespread industrial and construction components. The vast majority of finished products contain fasteners ranging from simple pins to threaded nuts and bolts to sophisticated self-retaining and self-locking nuts and clips. The global fastener market is worth
over $100 billion, with the largest users being the automotive, construction, heavy engineering, and aerospace industries.
Billions of fasteners are manufactured and installed every year. They play a critical role in the safety, reliability, longevity, and cost of manufactured products and construction projects. At first glance, there may not seem to be much difference between high-quality fasteners and low-quality, cheaply manufactured alternatives. After all, one hex nut looks much like another.
In fact, fastener quality differs enormously depending on manufacturing processes, materials, and the manufacturer's commitment to quality control. High-quality fasteners are stronger, more durable, and more likely to conform to standards and specifications. Choosing high-quality fasteners from a reputable manufacturer and distributor can help your business to produce safe and reliable products more efficiently.
5 Properties of a High-Quality Industrial Fastener
"High-quality" is an imprecise term, so let's look at the properties that distinguish high-quality fasteners from less well-made alternatives.
1. Materials That Meet Buyer Specifications
Fasteners are manufactured from a wide variety of materials including aluminum, bronze, stainless steel, carbon steel, and others, each of which are produced in a wide range of grades dependent on their chemical composition and intended use. For example, stainless steel fasteners are commonly made of 302 stainless, 304 stainless, 316 stainless, and 410 stainless. These stainless steels have varying proportions of iron, chromium, molybdenum, and nickel, resulting in fasteners with differing hardness, tensile strength, elasticity, corrosion resistance, magnetism, and other qualities.
Buyers select fasteners based on these qualities, but consistently manufacturing metal fasteners to precise metallurgical standards is complex and expensive. Low-quality fasteners may not meet materials quality standards such as the
ISO 15510:2014 stainless steel composition standard and other relevant standards relating to fastener materials and specifications.
2. Manufacturing Standards
Fasteners are subject to a number of regulations and quality standards. Chief among the legally mandated regulations is the
Fastener Quality Act (FQA). The FQA was created following a series of fatal product failures caused by low-quality fasteners. It requires fasteners to conform to the specifications as the manufacturer represents them and to conduct inspections according to standardized methods.
Beyond the strict legal requirements, manufacturers of high-quality fasteners also engage in quality verification and testing processes to ensure fasteners meet U.S. and international standards. These include fastener testing for hardness, shear forces, torque and prevailing torque, coating thickness, fatigue response, push out and pull out forces, and more.
Because of a high-quality manufacturer's stringent testing and quality control, buyers have increased confidence that their fasteners adhere to international fastener standards, such as ANSI and ISO standards for
screws, bolts, and studs,
nuts,
fastener materials, and
coatings.
3. Predictable Manufacturing Tolerances
High-quality fastener production is more likely to maintain consistent size and shape tolerances. For some parts, precise tolerances are not a primary concern. However, high-quality fasteners are essential in manufacturing scenarios where consistency and predictability are a priority. Out-of-tolerance fasteners may damage other parts and tools, slow production lines, and create weaker joints.
For example, out-of-tolerance bolts may have inconsistent threads, threads with burrs, incorrect shaft diameters, and other deviations from the specification. The obvious problem with over and under-sized bolts is that they don't fit in their intended hole or damage the hole's threads.
But slightly out-of-tolerance bolts and screws cause more subtle issues. Oversize threads require higher prevailing torque to install. Production line employees may fit the bolts to the specified torque, which will be reached before the threads are correctly seated. The result is an improperly installed bolt and an out-of-spec joint.
4. High-Quality Finishes
Finishes are another area in which high-quality fasteners excel. Finishes are applied to metals to improve a part's corrosion resistance and appearance. Common fastener finish processes include galvanization, electroplating, and conversion coating. High-quality fasteners provide consistent finishes across each part that conform to specifications and standards such as
ASTM A967/A967M-17.
Low-quality fasteners may exhibit unpredictable finishes with varying levels of environmental protection, appearance, and thickness.
5. Superior Quality Control
Quality control, also known as quality assurance, is a common factor running through the attributes of high-quality fasteners we've mentioned. Maintaining material standards, manufacturing tolerances, and superior finishes requires a significant investment in quality management systems.
Quality management systems govern manufacturing processes, operational procedures, inspection regimes, and audit schedules. Their goal is to ensure that every fastener adheres to strict quality standards.
One of the simplest ways to reduce manufacturing costs is to eliminate or decline to implement a quality management system. The consequence is often reduced control over materials and manufacturing standards, leading to low-quality output.
In contrast, manufacturers of high-quality fasteners are happy to invest in quality control because it allows them to consistently deliver the products their customers need and expect.
Risks of Using Low-Quality Fasteners
We've touched on a handful of problems that are likely to arise when manufacturing and construction businesses select low-quality fasteners, but what are the risks of using these parts in your business?
Low-Quality Fasteners Increase Costs
Low-quality parts can be less expensive, but what you save up front in procurement may result in higher manufacturing and service costs. Some of the ways low-quality fasteners increase costs include:
- Increased waste: Low-quality fasteners may be unusable because they do not conform to your business's internal standards and must be disposed of.
- Increased rework: Products may have to be returned to the production line for rework because they don't meet manufacturer or customer standards.
- Increased damage: Out-of-spec fasteners may damage other components and tools.
- Reduced manufacturing efficiency: Efficient manufacturing and construction require predictable, consistent components.
Unanticipated Weakness Contributes to Safety Hazards
Manufacturers choose fasteners to fulfill a specific role, but it's impossible to predict whether a low-quality fastener is adequate for the task. The worst possible consequence is joint failure that risks injury to workers or users. In many industries—aerospace, heavy machinery, automotive—fasteners are expected to be able to withstand extreme loads. An unexpected weakness in a single fastener can have catastrophic consequences.
Weak Joints Reduce Component and Construction Lifespans
Low-quality fasteners may corrode more quickly, crack more easily, and break more often. Compromising on fastener quality will result in a lower quality end product. These deficiencies are not obvious at first, but you can be sure your customers will notice when the equipment they rely on begins to fail faster and more frequently than expected.
How to Source High-Quality Fasteners
Huyett stocks a wide range of high-quality fasteners from leading manufacturers. We apply a rigorous
quality management system to all of our operations and conduct regular internal audits to ensure our commitment to quality is upheld. Additionally, Huyett is ISO 9001:2015 certified.
Our fastener selection includes:
- Pins and wireforms
- Nuts, bolts, and screws
- Washers
- Retaining rings
- Rivet nuts
- Engineered fasteners, including palnuts, self-locking nuts, self-retaining nuts, and panel and trim clips
View our
complete product range at huyett.com or
contact our Sales Team for more information.