- Huyett Marketing Department
- 01/06/2021
Unlike height, weight, and width, hardness is not a fundamental property of metal. Hardness is most closely related to tensile strength and is a reliable indicator of ductility and wear resistance. The principle of any hardness testing method is to force an indentor (penetrator) into a material sample under a specific load at a controlled rate and then measure the dimensions (depth or surface area) of the indentation. Unlike length, mass, or time which have exact measures, hardness testing is a comparative measure: accurate testing results can only be achieved with calibrated machines and previous test results taken from a material of known hardness.
In metallurgy, the hardness of a material depends on a combination of yield strength, tensile strength, and modulus of elasticity – the stiffness of a material and its ability to resist deformation under applied force. It is measured by indenting a small sample piece of material without destroying it.
Rockwell Hardness Test
The Rockwell hardness tester is essentially a machine that measures hardness by determining the depth of penetration of a penetrator into the specimen under certain fixed conditions of test. The penetrator may be either a steel ball or a diamond spheroconical penetrator. The hardness number is related to the depth of the indentation and the higher the number, the harder the material. A minor load of 10 kgf is first applied, causing an initial penetration. The dial is set at zero on the black‑figure scale, and the major load is applied. This major load is customarily 60 kgf or 100 kgf when a steel ball is used as a penetrator, but other loads may be used when necessary. The ball penetrator is 1/16" in diameter normally, but other penetrators of larger diameter, such as 1/8", may be employed for soft metals. When a diamond spheroconical penetrator is employed, the load is usually 150 kgf. Experience decides the best combination of load and penetrator for use. After the major load is applied and removed, according to standard procedure, the reading is taken while the minor load is still applied.
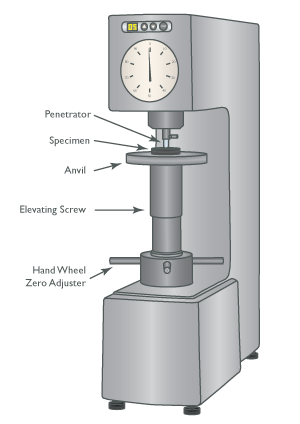
How a Rockwell Test is Performed
The Rockwell Hardness Number is the difference between two controlled indentations superimposed on each other.
The first indentation is made by a minor load applied to a steel ball or diamond penetrator. Then, without moving the penetrator, a major load is applied at a precisely controlled rate.
The hardness determination is made by measuring the additional indentation made by the second major force. The scale is proportionally inverse, so that the higher the number, the shallower the indentations, therefore the harder the material.
In the Regular (R) Rockwell Scale the minor load is 10 kilograms of force (kgf) and the major load is 60, 100, or 150 kgf. In the Superficial (S) Rockwell Scale the minor load is 3 kgf and the major load is 15, 30, or 45 kgf.
To ensure accuracy, the major load is applied with precise control and the penetrators are manufactured to exact tolerances. Each point on the R hardness scale represents 0.00008" and 0.00004" on the S hardness scale, making the precision and control of these tests readily apparent.

Avoiding Faulty Rockwell Tests
Proximity

Penetrator indentions must be spaced at least two indentation diameters from the edge of the work piece and a minimum of two indentation diameters from any other indentations to determine true hardness.
Material Thickness

Use a correct load/indentor combination relative to the thickness of the material. Tests will end up measuring anvil hardness and results will not be indicative of the true hardness of the sample piece.
No Stacking

Never stack multiple pieces of sample material. The interfaces between the strip will negatively affect the reading. Testing strip thickness needs to be at least 10x greater than the expected major load indentation depth.
Do Not Test Plating

Plated and finished samples must be tested in cross sections so that indentations can be made entirely in the base metal. Plating and finishing materials are typically harder or softer than base metals.
Calibration

Hardness testing devices must be kept in good working condition and calibrated every year. Use a test block of known hardness daily to verify that your equipment is calibrated correctly.
Curves

Bowed or twisted material will generate erroneous test results. Sample material must be flat and placed so that the bottom surface of the tested materials sits directly on the anvil.
Avoid Conversions

Converting test results from one hardness scale to another may produce faulty results. If a material is certified to a specific test's hardness, the final part should be tested on the same scale.
Tolerances

Hardness testing is toleranced with variables for plus or minus results. Refer to ASTM E10, ASTM E18, ASTM 392, ASTM E140, or ASTME E384 for specific allowances for your testing equipment.
Indentors

Round ball indentors must be round. While steel ball indentors are less expensive than their tungsten carbide counterparts, steel is more likely to flattern during tests of very hard material samples.
Surface Preparation

Test surfaces need to be smooth in order to produce accurate results. Rough surfaces will not allow the penetrator to create clearly defined, measurable indentations.
Test Surface

In order to achieve consistent, accurate results, the test surface must be parallel or perpendicular to the indentor.
Portable Testers

Handheld testers are cost‑effective and convenient, but they are not reliable substitutes for bench testing. They are best suited for comparison testing of unknown samples vs. known samples of the same type.